Évoquée il y a presque 10 ans, la digitalisation des entreprises et notamment de l’industrie manufacturière avec le concept d’« Industrie 4.0 » est une réalité en 2018.
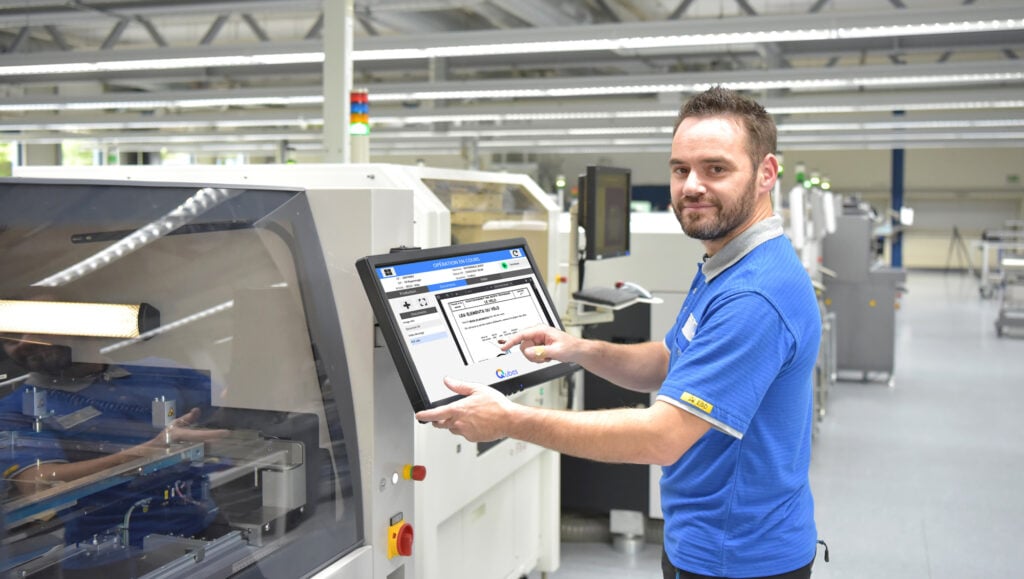
La transformation digitale dans l’usine est désormais incontournable.
A la recherche de gains de productivité, et également contraintes par les normes de plus en plus drastiques, par des exigences de transparence plus importantes, ainsi que par une concurrence intense et globale, les entreprises du secteur industriel n’ont pas d’autre choix que de faire le pas vers l’industrie 4.0 et en adoptant les technologies qui leur permettent d’augmenter la productivité tout en maintenant la qualité et traçabilité de fabrication.
Sans parler encore d’Usine Autonome et Usine du futur, ultime but à atteindre de cette transformation, l’implémentation d’un MES – Manufacturing Execution System permet déjà la dématérialisation des procédés de fabrication, au cœur de cette mutation, inévitable.
La dématérialisation des procédés du poste de production, premier pilier de la mutation.
Les entreprises industrielles s’appuient sur des procédures « papier » à toutes les étapes de fabrication, de pilotage des machines, de supervision des lignes et des pièces, de contrôle qualité, de supply chain, et de SAV, pour délivrer leur savoir-faire.
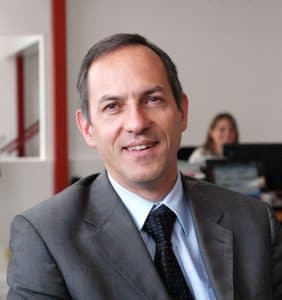
Christian Flachard, directeur commercial Creative IT
Le dossier de production pour un ordre de fabrication, tout droit issu de l’ERP consomme à lui tout seul 15 à 20 feuilles. Si on ajoute à ce dossier, les plans parvenant du bureau d’études et les fiches qualité qui sont des éléments documentaires indispensables au processus de fabrication, on peut facilement atteindre 50 feuilles de travail pour une pièce ou un lot. Les entreprises industrielles ne se posent plus aujourd’hui la question sur le fait que supprimer ne serait –ce que la moitié de ces documents est à la fois gage d’économie mais aussi un levier de progrès ergonomique et de productivité dans l’atelier.
C’est ainsi que la dématérialisation des documents d’ateliers place l’opérateur au centre de cette mutation numérique : on parle de poste opérateur multimédia
De quels documents s’agit-il ?
On parle de la digitalisation des fiches et procédés de fabrication, des procédures de tests, de la documentation des produits, des consignes de réglages machines.
Et en pratique ?
Tout au long de la chaîne de production, l’opérateur dispose d’écrans informatiques sur lesquels il est véritablement guidé : marches à suivre à cette étape du process, validation personnalisée dans le logiciel MES
Comment ces données sont-elles traitées par la suite ?
L’ensemble des données récoltées dans le logiciel MES sont transmises en temps réel à l’ensemble du système d’information de l’entreprise, ERP, PLM, GPAO, SupervisionDes plans à la validation de la conformité de la pièce, la dématérialisation des documents de l’ensemble de la chaine de production permet une continuité numérique indispensable à l’entreprise industrielle d’aujourd’hui quelque soit sa taille et son secteur d’activité.Elle permet non seulement d’améliorer la productivité, mais aussi de mieux produire, et de limiter l’erreur humaine.
Le poste opérateur multimédia : et le point de vue des opérateurs alors ?
Sans équivoque, les opérateurs et managers de terrain saluent l’arrivée de l’informatisation des ateliers.
L’informatisation des tâches et documents de production permet aux opérateurs d’afficher les instructions de fabrication, d’être aidé et dirigé dans leurs tâches.
Ils y voient des éléments de ré-assurance importants vis à vis du respect des processus, mais aussi de simplification et rationalisation de leur outil de travail, au moment où les exigences de productivité sont de plus en plus importantes. Ils apprécient aussi dans le partage des documents le transfert automatique des documents produits au service qualité. Les risques de perte d’information ou manquement à la traçabilité sont limités. Les remontées d’information sont fiabilisées.
Les utilisateurs sont véritablement guidés au travers de ce poste opérateur multimédia
Du côté des managers
Les managers usine et manager terrain plébiscite à la fois des gains de productivité, la fiabilisation de la chaîne bien sûr, mais aussi la capacité nouvelle à diffuser à l’ensemble des opérateurs des procédures et documents numérisés, dans une version toujours à jour, pour tous.
A l’issue de la journée de production, l’ensemble des informations saisies sont déjà numériques et donc exploitables directement sous la forme d’indicateurs, de reporting de performance.
Les Managers exploitent maintenant des données compilées, consolidées et complètes (smart data), en temps réel, sous la forme de tableaux de bord pré-paramétrés, facilitant les prises de décision.
Les managers disposent de tableaux de bords pré-paramétrés et consultent en temps réel la situation d’un ateliers, du poste,…
Entre gains de productivité, fiabilisation des processus de production, meilleur partage des informations et suivi des activités améliorées, les bénéfices apportés par l’informatisation des ateliers sont indéniables.
Le MES (Manufacturing Execution System), au cœur de la mutation digitale de l’entreprise industrielle
Un logiciel MES tel que Qubes est un système informatique qui collecte, en temps réel, les données de production de tout, ou une partie d’un atelier ou d’une usine. Une fois ces données collectées, elles permettent de réaliser plusieurs analyses concernant notamment la traçabilité, le contrôle de la qualité, le suivi de production, la maintenance, etc.La gestion des processus industriels par un MES permet ainsi de mieux organiser la station de travail, en rendant possible l’exécution numérique des différentes étapes de préparation et de validation des processus à travers un écran et non plus des procédures papiers.
On peut faire la même chose avec une GED ou PDM ? Non, pas vraiment.
La Gestion Electronique des Documents (GED) ou le PDM (Product Data Management) permettent la dématérialisation des documents et de simuler un workflow de ces derniers.En revanche, contrairement au MES, ces 2 types de solutions ne permettent pas de montrer tous les aspects des éléments de fabrication d’une pièce et surtout de suivre les corrélations entre tous ces éléments. En cas d’erreur dans une recette agro-alimentaire, les opérateurs ne recevront aucune alerte de ce type de solutions et poursuivront leur erreur jusqu’au processus qualité. trop tard.
Parlons concret : La dématérialisation du poste opérateur chez Nexter Systems et le MES Qubes
Nexter Systems, société du Groupe KNDS (KMW+NEXTER Defense Systems), est le leader européen de la défense terrestre. Nexter Systems répond aux besoins des armées de Terre française et étrangères, à travers la conception, le développement et la production de systèmes complets de défense, canons d’artillerie et engins blindés.
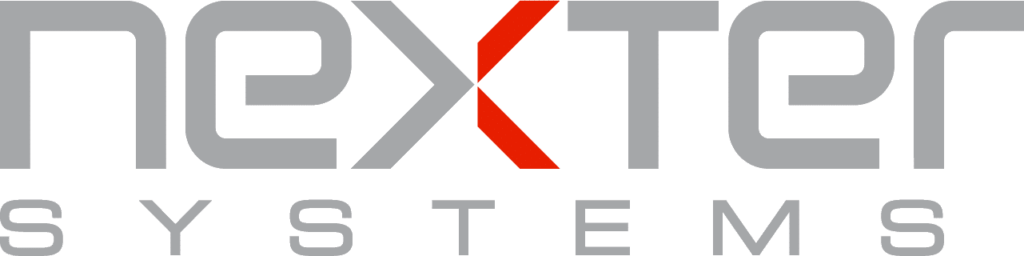
En 2014, 2 questions se posent à Nexter Systems : d’une part la société signe de plus en plus de contrats à options variantes, d’autre part, les faibles arrêts de ligne sont malgré tout coûteux et dégradent le taux de service client.
L’entreprise décide donc d’améliorer et de rendre agile sa chaîne de production, en regroupant l’ensemble de ses items informatiques dans une seule et même application : le MES Qubes.
En une année, Nexter Systems a informatisé ses ateliers en visant 2 objectifs : le management visuel et la continuité numérique.
Par le biais d’un affichage dynamique au sein des ateliers, les objectifs étaient d’optimiser les flux de production/logistiques et de responsabiliser les opérateurs sur ligne et les opérateurs logistiques.
Le MES en simplifiant les échanges de flux entre les différents logiciels du système d’information, a permis de supprimer le papier dans les ateliers, de redonner de la cohérence aux documents et micro-applications jusqu’à présent déconnectées du système d’information global et de s’approcher du point 0 des arrêts de ligne.
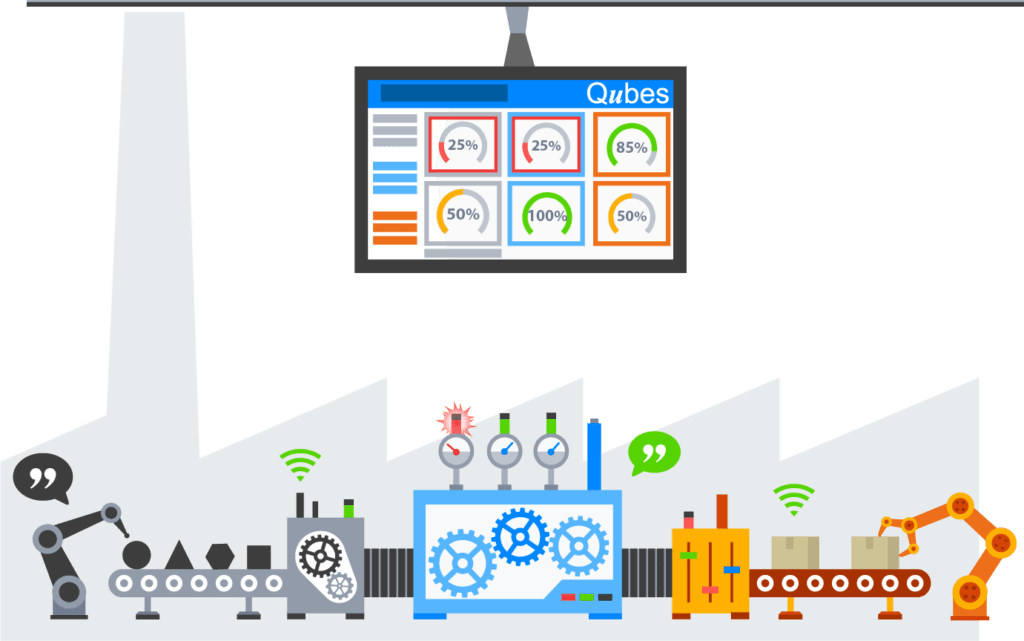
Schéma simplifié du système mis en place par Nexter Systems
Pour Guillaume Valette – Responsable du pôle Compétences Intégration et Systèmes de Production
La priorité des industriels en France pour la transformation digitale de leur entreprise passe en premier lieu par le suivi de production. Pour être opérationnel rapidement et fédérer les équipes terrain autour d’un outil ergonomique et convivial, Nexter Systems a mis en place une application de management visuel basée sur un progiciel de type MES. Le MES doit être le socle de l’Usine de demain, pour garantir la continuité numérique entre les différentes applications du système d’informations, et pour intégrer aisément au fur et à mesure les objets connectés.
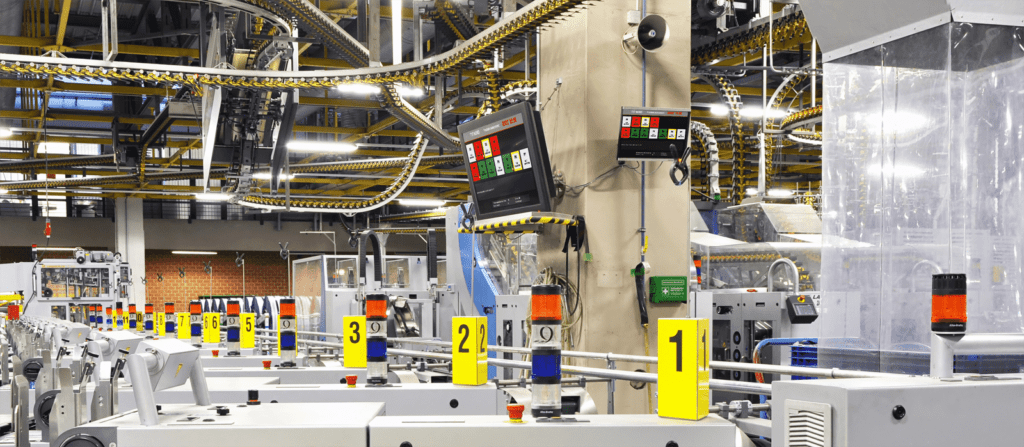
Longtemps rêvée, c’est devenu une réalité : la transformation digitale est en route, pour les petites, moyennes et grandes entreprises industrielles.
Envie d’en savoir plus sur la continuité numérique dans votre entreprise ? Contactez-nous !
Ressources complémentaires :