– Retour d’expérience de la société Gelagri Bretagne –
GELAGRI est l’un des plus importants producteurs européens sur le marché des légumes et produits élaborés surgelés. L’objectif prioritaire – au travers de l’informatisation de leurs usines – était d’assurer la traçabilité matière tout au long du process.
Le périmètre et les enjeux du projet
- Gelagri Bretagne a informatisé avec Qubes l’ensemble du flux depuis l’approvisionnement ligne jusqu’au pointage de palettes de produits finis et leur étiquetage.
- Approvisionnement pied de ligne par un cariste avec un PC à bord de son charriot : scan palette + scan ligne approvisionnée
- Entrée en ligne de conditionnement par un opérateur sur la plateforme d’approvisionnement
- Contrôles qualité en milieu de ligne, sur le produit fini : de nombreux contrôle aux attributs
- Validation des palettes produits finis : édition des étiquettes palettes, validation des palettes
Gelagri Bretagne conduit sa transformation numérique avec la solution MES Qubes
Témoignage de Gelagri Bretagne : informatisation des ateliers & conduite du changement
Quels avantages retirez-vous de l’utilisation de la solution Qubes ?
La mise en place de Qubes a provoqué des ajustements de poste : par exemple l’opérateur d’approvisionnement des lignes passait son temps à saisir des documents, aujourd’hui il a un rôle plus axé superviseur qu’acteur. En général les profils de postes évoluent vers le haut.
Le gros avantage de Qubes est son ouverture de l’outil de paramétrage au client, nous sommes complètement autonomes pour le développement de l’application entre autres pour le déploiement de nouveaux ateliers.
Les grandes étapes de la transformation numérique opérée chez Gelagri Bretagne
« Sur notre usine de Loudéac, nous utilisions un logiciel de suivi de production qui datait »
C’est en 2012 que l’idée de mettre en place un outil plus moderne avec de nouvelles fonctionnalités apparaît. « Nous nous sommes orientés vers la solution MES Qubes de Creative IT, notamment parce qu’elle était déjà implantée depuis une dizaine d’années sur notre site espagnol à Santaella en Espagne. Mais aussi parce que nous avons été séduits par son approche ouverte. C’est un système très paramétrable. Nos informaticiens ont la main sur le paramétrage des écrans tactiles et le développement de modules », poursuit-il.
Le déploiement de Qubes a été progressif, appuyé par l’installation d’une couverture wi-fi intégrale sur le site. Après les achats (en septembre 2014), les plats cuisinés (à Saint-Caradec en mai 2015), le contrôle qualité et le conditionnement (en 2016), c’est l’étape d’agréage (réception de la matière première fraîche) qui a été automatisée en septembre 2017.
« A chaque étape, nous avons listé les opérations. Ceci nous a permis de nettoyer nos procédures et surtout d’adapter les modules au flux physique pour faciliter le travail des opérateurs »
Les avantages de cette transformation numérique avec le MES
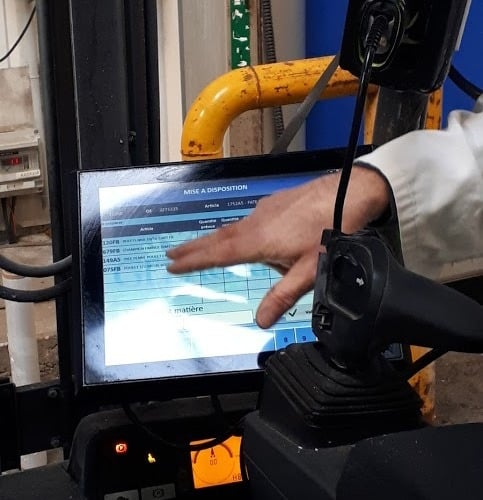
Mobilité
Les chariots assurant le transfert des légumes surgelés vers le conditionnement sont dotés de larges écrans tactiles et de « scannettes » résistantes aux vibrations et aux chocs.
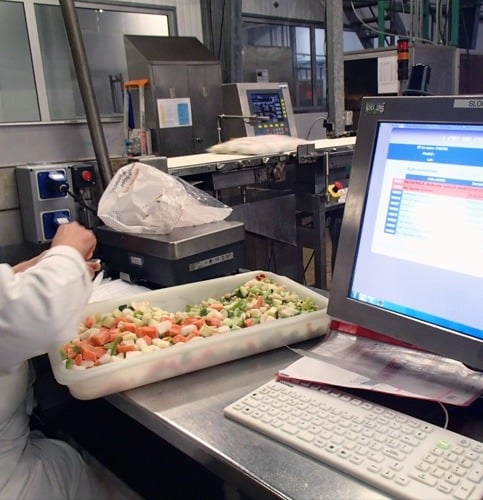
Qualité
Les auto-contrôles sont automatisés depuis septembre 2016. Le passage à Qubes a permis de remettre à plat la totalité des procédures.
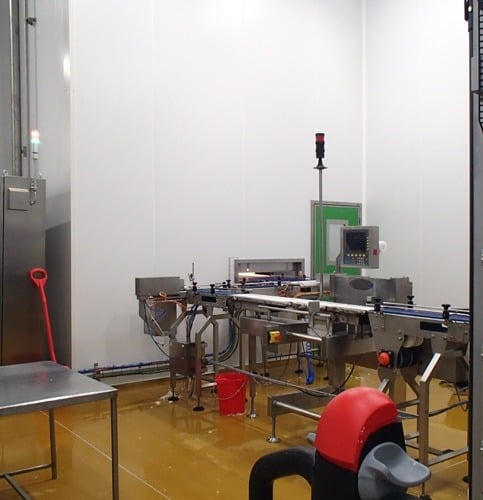
Acquisition
Dans l’atelier de préparation d’ingrédients pour les plats cuisinés, les balances sont connectées à Qubes pour une remontée automatique des données de pesée.