– Retour d’expérience : avec le logiciel MES Qubes, le groupe Prenveille optimise la collecte de ses données –
Spécialisé dans la sous-traitance électronique depuis plus de trente-cinq ans et implanté à Saint-Malo, à Lyon, à Granville (Manche) et à Grenoble, le groupe familial Prenveille s’est équipé en 2013 d’un logiciel de MES Qubes pour améliorer la saisie de ses données et renforcer l’ERP. Retour d’expérience sur plus de huit ans d’utilisation quotidienne sur le site malouin ASICA avant de basculer depuis le mois de juin dans l’ensemble des entités du groupe.
Reportage paru dans Production Maintenance n°74 | Septembre 2021 | Propos recueilli par Olivier Guillon auprès de Philippe Hourdin – responsable technique du Groupe Prenveille
Avec le MES, le groupe Prenveille optimise la collecte de ses données
Face aux géants bien connus du monde de la carte électronique, le groupe Prenveille fait figure de Petit Poucet malgré ses 220 salariés, ses trois sites de production et son site de prototypage grenoblois. Pourtant, au regard de la transformation digitale opérée au sein de ce groupe qui comprend trois entités bien connues du secteur – ASICA, CMS INDUSTRIE et Sicap – n’a rien à envier à ses confrères. D’ailleurs, à la fin de l’année 2012, lorsque l’équipe de Philippe Hourdin a initié le projet implémenter logiciel de Manufacturing Execution System, il faut bien avouer que le MES était encore un outil méconnu des industriels. « Disposant déjà d’un ERP utilisé partout dans l’entreprise, nous constations que celui-ci demeurait trop éloigné de l’opérateur de production et que les nombreuses saisies manuelles de temps de production, de suivi de qualité et de quantités se révélaient imprécises voire fausses », se souvient le directeur technique du groupe.
Philippe Hourdin
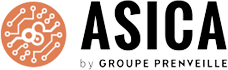
Âgé de 51 ans et de formation initiale d’ingénieur, Philippe Hourdin a passé cinq années passées dans l’industrie automobile avant d’intégrer ASICA en 2000 comme responsable méthodes. Aujourd’hui directeur technique du groupe Prenveille solutions électroniques depuis 2018, il est en charge des aspects qualité et techniques. En charge, avec l’appui de la direction Systèmes d’Information, depuis l’origine de l’étude et du déploiement de Qubes pour le groupe.
Nous souhaitions implémenter un système capable de collecter des données au fil de l’eau, le plus simplement possible à l’aide d’un terminal et pouvant s’interfacer avec notre ERP.
Nous travaillons à la commande et chez nous, les cycles de commandes sont très longs, surtout en ce moment avec les problèmes d’approvisionnement. De plus, entre l’ordre de fabrication et la production elle-même, le produit peut être amené à changer. Mais Qubes s’est très bien adapté à toutes nos contraintes, en particulier en matière de variation des OF.
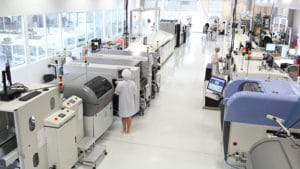
Des évolutions dans l’outil MES venant s’ajouter aux utilisations initiales
À l’origine, le MES a été choisi en raison de sa capacité à collecter au plus près de l’utilisateur les données de production, de temps et de contrôle qualité.
En cela, le logiciel Qubes a rempli ses objectifs initiaux d’autant que l’interface se montre très ergonomique. Le fait qu’il n’y ait plus d’opérations de ressaisie fait que nous avons gagné du temps et réduit considérablement le nombre d’erreurs, augmentant ainsi la qualité des opérations. Nous disposons également d’une bien meilleure connaissance des temps de production et d’une vision précise du process en cours et des quantités produites.
Cependant, après huit ans d’utilisation quotidienne, le groupe Prenveille a apporté de nouvelles fonctions au sein du MES. À commencer par la vérification de l’habilitation des personnes et de leurs compétences travaillant sur chacun des produits. Ces habilitations font l’objet de normes bien précises notamment dans l’aéronautique, le secteur du médical ou encore le ferroviaire. Autre évolution significative : désormais, les remontées d’informations ne sont plus seulement accessibles aux opérateurs mais aux chefs d’équipe, leur permettant ainsi d’avoir une vision d’ensemble des personnes qui travaillent sur ces lignes, des durées de chaque opération et d’obtenir des indicateurs de qualité, de quantité et de temps, avec un système d’alerte associé.
Nous avons même ajouté une messagerie afin que l’opérateur et le chef d’équipe communiquent rapidement
Un logiciel MES au coeur de la transformation digitale initiée par Asica
Pleinement opérationnel depuis 2013 sur le site ASICA à Saint-Malo, le logiciel MES Qubes a également été déployé sur le site SICAP de Granville en juin et est en cours de déploiement sur le site CMS INDUSTRIE de Lyon, une étape qui prend un peu plus de temps du fait de l’utilisation d’un autre ERP que celui du siège. Parmi les autres grands chantiers du groupe figure bien sûr la poursuite de la digitalisation, projet qui impacte toutes les entités et les services de l’entreprise, jusqu’aux relations avec les clients et les fournisseurs ; mais aussi, davantage liée au process, la connexion de tous les robots 5 axes chargés de la pose des composants CMS, et dont l’objectif est de les interfacer avec l’ERP puis avec le MES. Enfin, à terme, le logiciel Qubes fera également l’objet d’évolutions à différents niveaux – traçabilité, logistique interne, conditionnement et suivi des flux ; « celles-ci ne sont pas prioritaires mais n’en sont pas moins planifiées ».
Nous avons l’immense plaisir de partager avec vous le reportage réalisé sur le site industriel Asica. Découvrez au travers de cette vidéo les coulisses d’un vaste projet de digitalisation d’un groupe industriel remarquable.
Autant de projets dont le MES fait désormais partie intégrante. « Nous constatons une montée en puissance de la qualité et de la traçabilité, sujets faisant l’objet de demandes croissantes de la part des industriels, précise Marc-Antoine Sérillon, responsable Marketing de Creative IT. C’est pourquoi en tant qu’éditeur nous travaillons également sur ces sujets notamment en nous entourant de partenaires comme récemment avec la société Coppernic ».
Pour retrouver en intégralité la réflexion de cette nouvelle approche de la transformation digitale des usines, il suffit de revisionner notre série de webinar sur notre chaîne Webikeo.
Comment déployer le digital dans vos usines de façon rentable ?
Ressources complémentaires :
- Faire de sa transformation digitale industrielle un succès : grâce aux retours d’expérience et à l’écoute active des différents acteurs de l’industrie, nous proposons une méthodologie plus proche des attentes des industriels face aux défis de la transformation digitale industrielle.
- Échangez avec l’un de nos experts de votre projet de transformation digitale industrielle
- Les clients du logiciel MES Qubes
- Creative IT et Coppernic associent leurs expertises autour des solutions RFID pour répondre aux enjeux de la traçabilité industrielle