– Issues, best practices, new technologies –
Industrial challenges are no longer limited to meeting delivery deadlines, reducing inventory or optimizing productivity. Improving customer relations is a major source of profit. Having precise information on the products manufactured and on their routing is a source of differentiation and a commercial argument.
Article outline :
- Definition of traceability applied to the industry and maturity of manufacturers
- The regulatory framework: industrial issues?
- Expert opinion in industrial traceability
- Good Practices on the computerization of traceability
- Update on traditional technologies and new possibilities offered by IoT and BlockChain
Traceability in production: what is it ?
We speak of total traceability when we are able to identify all the components and information of a product from the suppliers to the customers.
Traceability is a process that follows a product throughout its life cycle, its value chain.
The traceability in production concerns all the operations from the entry to the exit of the factory :
- Identification of products, components and materials throughout the manufacturing chain, from receipt to shipment
- Logistical traceability, which aims to track inventory movements in the factory
- Complete traceability of production operations :
- Material traceability: components (or materials) consumed and produced
- On the participants (operators, maintenance technicians, quality agents,…)
- Traceability on equipment and tools
- Process traceability with automatic time stamping of each step of your process
Industrial maturity: where do we stand?
The maturity of companies is very different depending on the industrial sector.
The agri-food, pharmaceutical, automotive and aeronautical industries are making rapid progress, whereas other industrial sectors are not making traceability in production their priorities, despite the fact that new technologies are creating new business models (e.g. product customization).
According to the industrial sectors, the needs of traceability can be different :
DIn the food industry, there is a strong demand for material traceability. On the one hand, it is a question of qualitative traceability (recall of products or batch in case of sanitary alerts on a raw material) and quantitative traceability (respect of the recipes, reliability of the industrial cost price).
Manufacturers in the cosmetics, pharmaceutical and medical device industries are more concerned with process traceability: recording quality controls throughout the process, highlighting non-conformities in order to generate the batch file (batch release or destruction).
Finally, in the manufacturing industry, traceability projects aim at a rigorous follow-up of the traceability of equipment (tools, machines), a very precise marking of all components (serialization).
Example of the implementation of a traceability software in production: Gelagri Bretagne
Interview with Mr. Paul Le Bescond, IT Project Manager at Gelagri Bretagne
“Our primary objective was to ensure the traceability of the material throughout the process.
We also wanted to carry out and record quality controls on the product. Today, we have computerized the entire flow from the line supply to the pallet checkout of finished products and their labeling :
- Foot of line supply by a forklift operator with a PC on board his truck: pallet scan + line scan
- Entry into the packaging line by an operator on the supply platform
- Quality controls in the middle of the line, on the finished product: numerous attribute controls
- Validation of finished product pallets: edition of pallet labels, validation of pallets”.
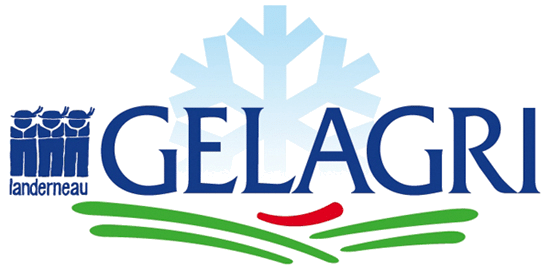
Gelagri Bretagne
860 employees on 3 sites
Commercial brand: Paysan Breton
The regulatory framework of traceability in production: a strategic issue or a constraint for manufacturers?
The various health crises that have occurred in recent years show that traceability remains a concern.
However, some industries can proudly display a flawless traceability, clearly making it a selling point: for these manufacturers, traceability throughout the value chain is a strategic issue. Traceability constitutes today an opportunity to (re)create a link with the final customer and bring him added value. It is the same for convincing a prospect or a customer during the visit of the factory. Traceability screens in production and quickly executed traceability exercises become a marketing differentiator.
Why do manufacturers need traceability in production?
First of all, industries equip themselves with traceability software in production for external needs :
- regulatory needs: compliance with the standards in force in the sector of activity
- business needs: the ability to meet customer specifications / requirements
- security needs: serialization makes a product unique and inhibits counterfeiting
- sanitary needs: the identification of batches of finished products makes it possible to recall defective products quickly and at lower cost.
- maintenance needs: for machine manufacturers, real-time monitoring of the products used allows greater reactivity
- planning needs: anticipating low stock levels avoids disruption
Then, manufacturers computerize their production traceability for internal purposes:
- process traceability: continuous improvement
- dematerialized manufacturing file, productivity gains: being able to give the end customer all the information specified in his specifications
The regulation around the traceability in production
International standards define the respect of traceability norms in production:
Food industry requirements: ISO 22000, IFS, BRC
Requirements of the cosmetics industry: ISO 22716
Requirements of the pharmaceutical industry: GMP and FDA 21-CFR-11
Requirements for medical device manufacturers: ISO 13485
Requirements of the aeronautics industry: ISO 9001
It is the precise knowledge of the inputs and outputs of the production chain that will allow the company to inform its customers on the details of the goods sent by guaranteeing traceability. If the industrialist has not ensured the traceability of his components, it stops at him with all the responsibility and the associated costs.
Expert opinion in industrial traceability
Propos de M. Olivier Barnet, Chef de projet Creative IT
Comments from Mr. Olivier Barnet, Creative IT Project Manager
Industrial companies – particularly in the manufacturing, pharmaceutical and food sectors – use Manufacturing Execution System (MES) tools to address a wide range of tracking and traceability issues. This is especially true in the food industry, where many manufacturers are using MES, especially to trace raw materials.
It is a question for the food industrialists of carrying out a qualitative traceability, in other words a traceability of batches in order to ensure as quickly as possible a recall in the event of problem – in particular sanitary -, and a quantitative traceability, which takes into account the price of the raw materials in order to better control the impact on the price of the final product
If the M.E.S. responds essentially to sanitary needs in the food industry, it is for health and safety issues that it intervenes in the pharmaceutical industry.
The pharmaceutical industry is undoubtedly the one that has pushed the process traceability part the furthest with quality controls in production ensuring process traceability of the most critical batches. With the MES Qubes, one of our customers has succeeded in tracing each product containing allergens. The solution deployed allows the operator to be alerted on the material to be used during preparations to avoid cross-contamination of allergens between the different components/materials.
As for the manufacturing sector, it uses M.E.S. more and more for industrial traceability needs, in particular in maintenance, as is the case with machine and machine tool manufacturers, where tools must be regularly checked, maintained and calibrated. It is the same for the molds and the parts which will compose the machines which, after a certain cycle of use, will have to be imperatively replaced.
MES allows manufacturers to reduce preventive and systematic maintenance operations in favor of predictive maintenance
Good Practices on the computerization of traceability
How does MES software meet the challenges of traceability in production?
A production traceability project goes hand in hand with the implementation of an MES software. We therefore try to meet various objectives of continuous improvement :
- Equip yourself with an ascending and descending computerized traceability to save time when searching for a batch or a component: during traceability exercises or during crisis situations (product recall, internal verification operations), for compliance reports requested by customers, for certification audits or customer audits.
- Making the industrial process more reliable the fact that operations are traced forces operators to respect ranges and bills of material and ensure product conformity, and also makes industrial cost prices more reliable
- Save time on problem escalation to reduce non-conformities: processes guide operators, drift detectors alert operators to potential risks, deception devices improve product safety.
- Eliminate paper on the shop floor to reduce errors (re)entry: this involves the dematerialization of processes and document management (EDM = Electronic Document Management).
Example below with the generation of a manufacturing file made up of all the traced production operations: traceability of weighing and quantities, material traceability, process traceability (execution of OF: ranges, nomenclatures, etc.), traceability of resources (teams, operators, etc.), traceability of quality controls.
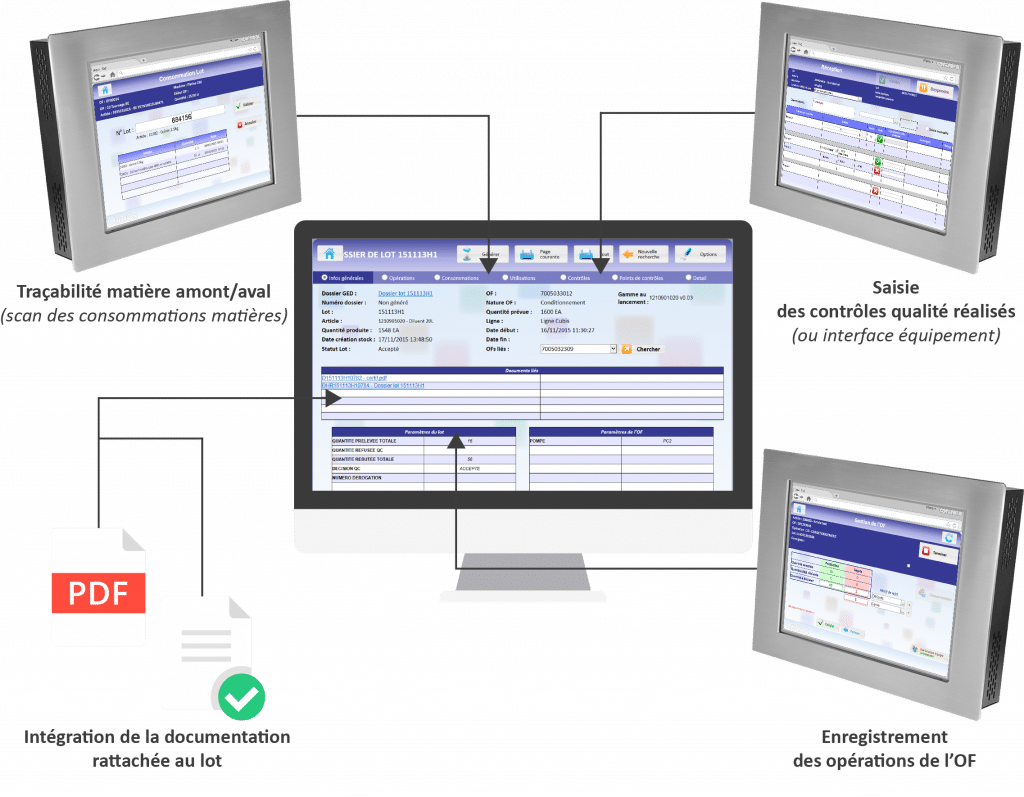
How to start your traceability software in production?
One of the first challenges is to choose a simple, intuitive and ergonomic software that will allow to value the work of the operators in workshops.
Making operators aware of their responsibilities
Any traceability computerization project starts with the involvement of end users who will contribute to the implementation of an application they will feel comfortable with. It is through this awareness and involvement of the field teams that the quality of the information provided throughout the process is ensured.
Industrial organization prior to the implementation of a traceability software
Regardless of the traceability software chosen, the implementation and design of such an application should not be overlooked. It is imperative to have an internal team that will coordinate the relations and deliverables between IT service providers, solution editors, and all the project’s internal interlocutors (without forgetting the end users). This notion of industrial organization is essential, without which the risk of not respecting the schedule increases with each missed organizational step.
Specific application or market standard ?
Specific application or Rather than starting from scratch, the industrialist can choose a traceability software in production that has already been audited according to business standards. In this sense, MES solutions meet these standards and are an excellent intermediary :of the market ?
- to provide the ERP with reliable data thanks to ergonomic man-machine interfaces
- to exchange with existing automats and machines
Thanks to their interoperability and scalability, MES solutions allow to structure traceability projects while keeping the possibility of functional additions (TRS functions, CMMS, etc.) afterwards.
Why not handle industrial traceability through ERP ?
ERP software is fully capable of ensuring industrial traceability.
However, the way ERP works does not allow the industrial process to be dematerialized.
This means that the industrial traceability managed in the ERP consists of (re)entering paper documents circulating in the workshops, generating additional labor costs and increasing the risk of entry errors.
Only MES software has the capacity to dialogue with the machines to collect process data and restore traceability.
The quality of a production traceability project and the implementation of an MES solution depends on the sum of these seemingly insignificant elements.
Update on traditional technologies and new possibilities offered by IoT and BlockChain
Traditional identification and marking technologies – barcode, Datamatrix RFID – are now widely deployed in the French industrial landscape.
The massive arrival of connected objects (IIoT or Industrial Internet of Things) in the industry allows to collect more and more data in the workshops. To exploit IIoT, you need a connected object, a communication network and an IoT platform.
Blockchain technology also contributes to the traceability of the supply chain. The advantage of this collaborative technology is the organization of information sharing through the authenticity and security of transactions made in the chain.
However, the Blockchain does not guarantee the veracity of the information.
The collection of data made in the Blockchain is perfectly auditable and could guarantee the traceability in production.
Beyond that, connected objects and blockchain are just technologies that offer new ways to collect data: statistical analysis is needed to make this data talk.
MES solutions allow to go further in the exploitation of these data by allowing to contextualize them (OF, batch, team, equipment).
Glossaire de l’article :
Techniques de l’Ingénieur magazine website | Traceability practices and methods in industrial companies
Ressource complémentaire :